本文轉載自微信公眾號:Amao_eda365,原文作者陶源。已獲得轉載授權。
要說 Air pods Pro 火在哪裡?除了 Air Pods 的產品其優越的佩戴體驗舒適外,個人覺得最大的亮點就是其兩項黑科技:
1. |
主動降噪 |
---|---|
2. |
SiP 技術 |
1. 主動降噪
據蘋果官方表示,Air Pods Pro 的外向麥克風可以檢測外部聲音並分析環境雜訊。隨後 Air Pods Pro 具有創建等效的抗雜訊功能,以消除背景雜訊。另外,Air Pods Pro 還擁有面向內部的麥克風,可檢測剩餘噪音。據悉,噪音消除功能,每秒可連續調整 200 次聲音信號,有效提升降噪效果。
這次 Air Pods Pro 搭載了三顆麥克風:外向式麥克風(波束成形麥克風),內向式麥克風和通話麥克風(波束成形麥克風)。其不僅可以消除外部的雜訊,而且可以抵消耳蝸內的雜訊;據業界回饋,其降噪功能特好,特別是坐飛機的時候。
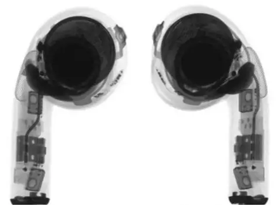
圖 1:Air Pods Pro
從技術上看,不僅與其自身晶片強大的資料處理有關,也與其優越的 MIC 性能有關。
※ 據分析其耳機內部用到的 MIC 全部來自於歌爾股份。而這些正是通過使用 SiP(系統級封裝)技術來實現。
2. SiP(System in Package)技術
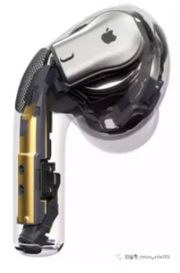
圖 2 :產品透視圖
網上有很多關於 Air Pods 的 SiP 介紹,及學習材料,如 SIP 工程入門的書藉有新出版的《晶片 SIP 封裝與工程設計》等。聽 SiP 會議,大咖們都喜歡從摩爾定律談起?(摩爾定律指:積體電路上可容納的元器件的數目,約每隔 18-24 個月便會增加一倍,性能也將提升一倍)再從堆疊、埋入、先進封裝、扇出,TSV 等介紹 SiP 可以延續此定律。
但內容一般會較高大上大方向講,極少有深入的設計分析,本文則以分析 Air Pods Pro 採用了的 SiP 先進封裝技術,可以實現此產品的小型化等非常接地氣的實用技術分析。
3. Air pods Pro 與 SiP 相關的先進技術
下面將分別分析 SiP 內部所用的技術及通過什麼方法可以使 Air Pods Pro 產品如此精細小。
3.1 Air Pods Pro 所用的 SiP 模組技術探討
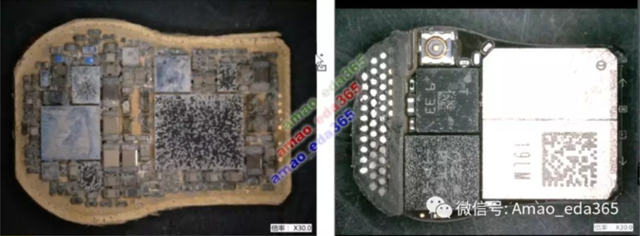
圖 3:Air Pods Pro 拆解圖
TOP 面
Top 面(即 Mold 面) Mold 裡面沒有 WB,沒有堆疊,沒有埋入,沒有 TSV,沒有 3D Fan-out 等等,簡單來看就是一個高密的 SMT + Mold + EMI Shielding 結構。
1. SMT:
內部一共包含了 80-90 個電阻、電容和電感器件,最大尺寸 0402(4 個),最小 01005,沒有 0603 器件,也還沒有用到 008004 器件,但其器件到器件間距 01005/01005 間距 100um (實際測量值,考慮到器件的公差及設備的精度,設計值可能是 80um);實現了真正的 High Density SMT。
2. WLCSP:
內部 IC 全部為 WLCSP 器件,最小的 Pitch 為 360um,焊球高 150um;其他均為 Pitch: 400um; 這個規格,組裝能力強一點的封裝廠應該都具備此能力。
3. Mold:
SiP 採用異形設計,與常規見到的矩形的封裝不同,需要採用 Selective Molding,單獨設計 Mold 異形模具,一套 100 多萬,而且週期長:3~4 個月。
TOP 面採用 MUF 工藝,Under fill 也不用了,可以進一步地縮小模組的佈局空間;另外,據分析,其 Moldingfiller size 特小:5~8um;對 Mold 材料的選擇和 Mold 的設備都有特別的要求。
採用 Mold 工藝將器件塑封在基板上,既可以提高 SMT 的可靠性,提升整個模組的硬度,同時也為下一步的 EMI Shielding 提供支撐面。這也是 Air Pods SiP 與其他的 PCBA 的技術差異。
4. EMI Shielding:
EMI Shielding 中常用到共形遮罩,其實現的方法有多種,如:電鍍、濺射、噴塗等等,它們作為一種新的電磁遮罩的技術被廣泛應用在射頻、存儲等電子封裝上。就是在封裝的表面形成一種薄薄的金屬層,以此來遮罩內部器件免受外界干擾,同時也遮罩 SiP 內器件和電路對外界的干擾。
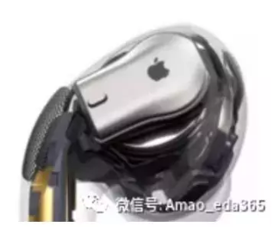
圖 4:Shielding 效果
共形遮罩有 Conformal Shielding 和 Compartmental Shielding 兩種,其技術優勢網上材料較多,這裡不再深入。
Air Pods Pro 採用的是 Sputter 工藝(SUS-Cu-SUS),Conformal Shielding,都是標準的 Sputter 工藝。
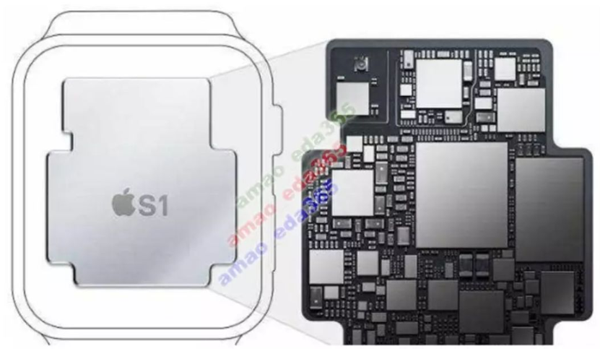
圖 5:Shielding Sputter 效果
5. SiP 共形遮罩的優點:
共形(Conformal)和劃區(Compartmental)遮罩方案應用靈活廣泛 |
|
最大限度減少封裝中的雜散和 EMl 輻射 |
|
最大限度減少系統中相鄰器件間的干擾 |
|
器件封裝橫向和縱向尺寸增加幾乎為零 |
|
節省系統特殊遮罩罩部件的加工和組裝成本 |
|
節省 PCB 面積和設備內部空間 |
BOTTOM 面
BOTTOM 面,比較簡潔,包括一個較大且 EMI Shielding 的器件,兩個 SENSOR 器件,一個 Interposer ,射頻天線連接器和它對應的 π 形匹配,還有其他的 5 個分立的阻容感器件。
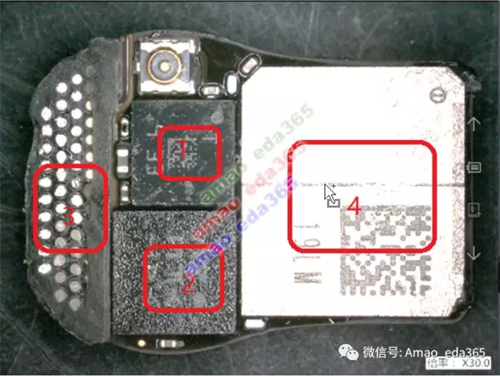
圖 6:背面元件
1. 上圖中數字 1 和數字 2,為 2 顆感測器
一顆語音辨識加速感應器,一顆運動加速感應器(ST 意法半導體的語音辨識加速感應器,說明上行通話降噪,特別針對風噪和環境雜訊。Bosch 博世的運動加速感應器,與光學感測器配合,檢測使用者佩戴狀態)。
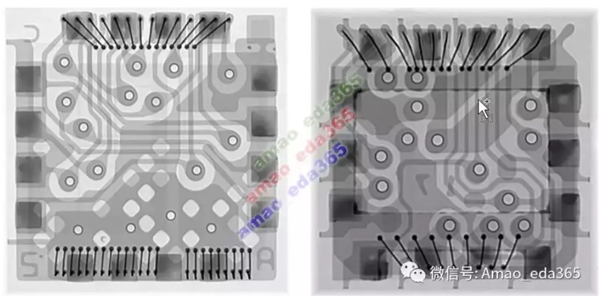
圖 7:感測器內部走線
對於感測器,兩層 Substrate 加 WB+ Mold,LGA 封裝,內部非常簡單,一看上圖就明白。
2. 數字 3 處一個基板 Interposer
應該是 Air Pods Pro 的一個亮點,用於信號的測試點,和與 FPC 的連接。
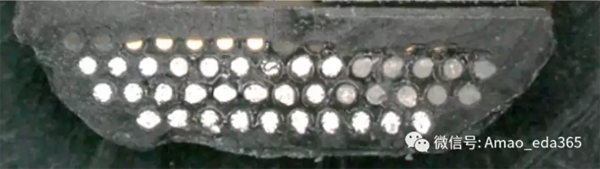
圖 8:基板 Interposer
TWS 耳機中由於結構及其它的一些設計要求,不可以把所有的器件都放在主機板上,如 MIC、SPK、位置感應器等,必須放在結構配套的位置,這樣,就需要用到 PFC;常見的 PFC 與主機板的連接有:B2BConnector、Hot bar、 ACF ,還有近幾年比較流行的軟硬結合板;各有自身的優缺點。舉例如下:
B2B Connector: |
|
工藝比較簡單,很多產品都用這種,但是缺點 PIN數少,面積大。 |
|
軟硬結合板: |
|
省掉了連接器,Pin 數也不受限制,但成本高。 |
|
Hot bar,ACF: |
|
工藝比較好實現,但對 Pitch 有要求,比如:pitch至少 0.8mm;同時良率不是特高;同時由於熱壓的影響,周邊的器件距離 Hot bar 工藝區域至少 1mm 的淨空,這個對於小型化的穿戴產品是致命的。ACF 工藝 ,沒那麼多要求,但其對於 Pitch 有一定的要求,良率還不是很高。 |
|
Interposer: |
|
而 Air Pods pro 的這個 Interposer,採用一個尺寸約為 2*7*0.7mm 的有機基板轉接板,底部採用 BGA 焊球與大的基板連接;同時將焊接點抬高,從而避開了淨空要求。在 Interposer 上佈置了近 50 個焊接點和測試點,Pitch:0.425mm,焊接點採用滿整列設計,非常密集;既可滿足測試的要求,也能滿足 SMT 的要求。Interposer 與周邊器件只要滿足 SMT的工藝要求:100um 即可;大大減少了焊接點和測試點的占板面積。 |
3. 數字 4 處標注的器件
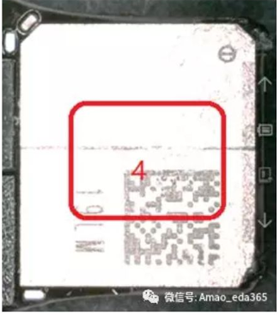
圖 9:複雜 SiP 元件
這是 Air Pods Pro 的一顆核心器件,一個 Dual Side Mold BGA 的 SiP 器件,猜測是其 PMIC 和 DSP 的結合。
這顆 SiP 器件有較大的難度,Top 面是 FC + SMT + MOLD + EMI shielding;Bottom 面是 EpoxyDie Mold + Ball。
結構堆疊方式類似如下示意圖:
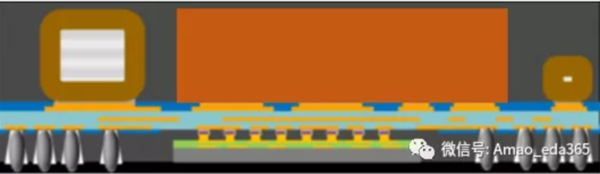
圖 10:堆疊結構方式
對應的工藝描述如下:
TOP 面內部 SMT + FC ,難點在於其整體的 Mold 高度 350um,Mold 與 Die Top 的 Gap 為 50um (現在一般的工藝能力都是 100um 以上);TOP 面採用了共形遮罩,Conformal Shielding (至於上面為什麼有一條分割線,後面再詳細介紹),和大 SiP 的工藝一樣,Sputter 工藝,很成熟。
BOTTOM 面為 Epoxy Die Mold + Ball :首先進行 Mold,然後通過鐳射將錫球焊盤裸露出來,最後才進行植球;中間的 DIE,為先進行整體的 Mold,再通過研磨的方式將 DIE 的表面裸露出來,用於散熱。
中間的基板採用 Coreless 工藝,6 層板厚度 200um;
整個 SiP 的高度為 750um 左右,與基板 Interposer 高度相當。
這顆晶片來料就是 SiP 器件,對上游的封裝廠(具體廠家不明)的工藝極具難度挑戰。Air pods Pro 組裝廠家 Amkor 只需要完成把這顆 SiP 組裝到大的 SiP 即可。
4. RF 連接器
Bottom 面還有一個重要的器件—— RF 連接器;與一般常用的天線彈片設計不一樣,Air Pods Pro 採用了一個 SMT 的天線連接器,天線設計在耳柄上,通過連接線和連接器與主 SiP 連接。
天線設計為了保證天線的性能,往往要求天線對應區域保持一定的淨空空間,如果天線放在耳蝸內,則天線投影區域及天線彈片對應區域都需要淨空,且不是單面這麼簡單而是雙面及所以內層都要求淨空;這種對於 TWS 的設計極具挑戰;但 Air Pods Pro 現在這種設計,對 SiP 模組影響降到了最低,只需要連接器對應區域下面 3 層進行淨空即可,背面一樣可布器件,可走線,大大簡化了 SiP 的設計,間接實現了小型化。
對於天線的匹配:放在 SiP Mold 區域外面,畢竟 Mold 材料對RF性能會有影響,且放在裡面不可調。
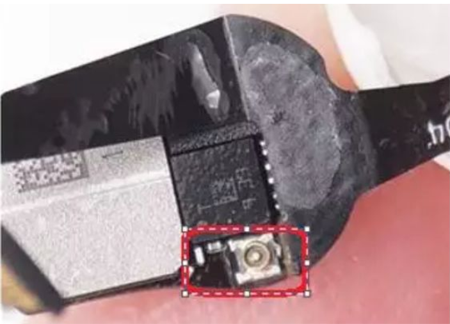
圖 11:RF 連接器
5. 基板
上面介紹了內部器件接下來介紹基板。它是 8 層基板,Low CTE 材料,常規設計,厚度 300um(Core:50um); Line W/P: 40/40um; Via:80/140um 3+2+3(任意階)。
3.2 Air Pods Pro 產品減少尺寸的綜合考慮
前面介紹了 Air Pods Pro SiP 內部包含了的元件等,相信讀者對內部的器件及結構有了一個較為明確的瞭解。現在介紹 Air pods Pro 為什麼可以做得很小。
自從 Air Pods Pro 爆火之後,很多公司都在提:我們也要用 SiP 技術,做一款和 Air Pods Pro 一樣的小而輕,功能強的 TWS 耳機。
相對于我們傳統的 PCB + SMT 和我們的軟硬結合板,都是有機基板加 SMT,SiP 工藝有它的技術優勢:下表為一個 PCBA 和 SiP 的對比,可大家以後設計時參考借鑒。
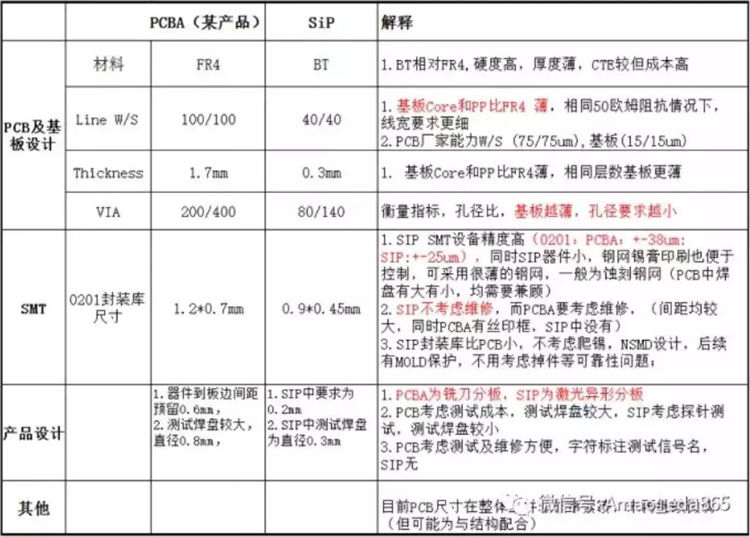
表 1:PCB 與 SiP 比較表
Air Pods Pro 採用了 SiP 模組,對於產品的小型化有較大的幫助。
4. AirPods Pro 中 SiP 對系統及工藝的考慮
Air Pods Pro 產品應用了 SiP 裡面的許多項技術與工藝,經過前面詳細技術分析與介紹,對於下面所提的數字 1-5 標的問題進行技術分析。
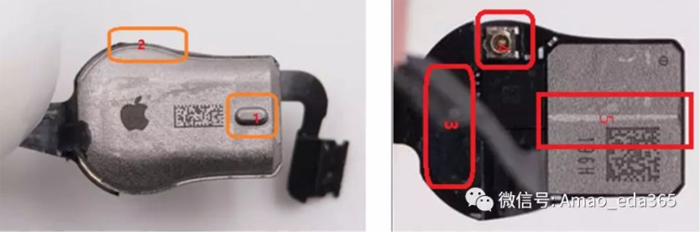
圖 12:分析標注位
4.1 數字 1 處為什麼有一個凸起,其主要功能是什麼?
乍看起來像一個按鍵,其實不是,而是為了固定 FPC 用;它出於從整機的角度,SiP 模組要求等考慮,此凸台高度為 360um。
但對於一個這樣的小需求,在 SiP 模組的設計和工藝帶來的難度卻不簡單,SiP 模組 Mold 工序需要考慮模流,需要考慮凸台的脫模的角度,同時還要考慮這個凸台的磨損對整體外觀的影響等等。
※ 據 Apple 產品工程師回饋,蘋果對外觀的卡控非常嚴格,同時外觀不良也是整體不良率中的非常大占比)。
4.2 數字 2 處模組表面為什麼是銀色,而模組的側邊不是銀色?
前面的技術介紹時已提過,這是因為模組採用了共形遮罩中的 Sputter 工藝,表面的銀色是做了 EMI Shielding。EMI Shielding 由於採用與 Mold 共形的原因,厚度較薄,正面鍍層厚度在 6~8um 之間,側邊的鍍層厚度在 4~6um 之間。幾乎不增加模組的高度;這與我們常規的金屬遮罩高度相比,可以明顯降低整體的高度,金屬遮罩蓋 常規值 0.15~0.2mm; 內部安全高度 0.2mm,外部安全高度 0.2mm;共形遮罩與金屬 LID 相比,高度上至少可以降低 0.5~0.6mm。
這麼精確要求的一個結果就是成本增加了,這也是為啥【水果】這麼貴的原因。
那為什麼銀色區域沒有到邊緣呢?
常規的 EMI Shielding 都是器件切割成 Unit 後,採用 Carrier 進行 Sputter 工藝,器件的側邊也可以濺鍍上一層金屬;Unit 側邊露銅,形成一個完整的蓋子整體;但效率低,同時需要採用定制 Carrier,成本也比較高。
Air Pods Pro CFS 工藝為 Panel 狀態時作業,然後進行 Laser Cut,故 EMI Shielding 沒有濺射到側邊。
或許你會問:那信號不是從側邊洩露出去了嗎?
當然不會,基板設計時,會在基板的週邊預留一圈銅皮和 GND 的過孔,EMI Shielding 與表面的銅皮相連。當然了,這些,都可以通過電磁模擬進行分析和評估。
Panel level CFS, UPH 較高,可間接降低整個 SIP 組裝的加工成本。
4.3 產品中數字 3 處這個凸起的圓弧形作用是什麼?
前面介紹使用基板 Interposer ,既省掉了 B2B 連接器,又實現了高密的測試點和連接焊盤;同時,還解決了 Hot bar 對於工藝避讓區域的要求限制。
通過可調節的高度(其高度可根據整體結構的要求進行設計,從 0.2~2mm 均可),有助於後續 FPC 的彎折,固定等等。
4.4 產品中數字 4 處的連接器有什麼作用及特點?
天線射頻連接器底座,其獨立藍牙天線採用 LDS 技術,放在耳機耳柄上,SiP 模組中只是放置了一個天線連接器底座,8 層板,只禁布了其中的 2 層,背面走線,佈局器件。這與目前很多公司的 TWS 耳機中天線彈片完全不一樣,很多公司的 TWS 耳機不但要求投影區域全禁布,而且有的還不止一個天線彈片,如這樣的限制,則更加難把模組做小!
而且,其射頻連結非常簡潔,除了一個 π 形匹配外,沒有其他的 PA、Filter 等器件及其匹配。
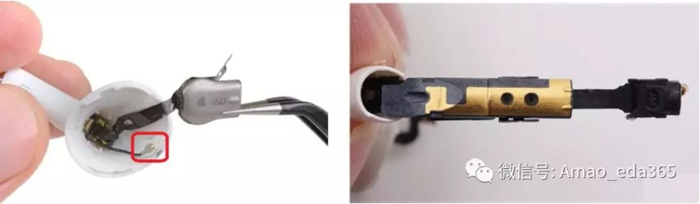
圖 13:天線
4.5 這個晶片數字 5 表面處為什麼會出現一條線?
這顆器件其 Mold 面為一階梯形,上半部分比下半部分低 100um(上半部分Mold 厚度 250um,下半部分 350um) ; 這 100um 的高度差目的是給 FPC 留出空間,用於放置下圖示號 A 的 FPC。
前面已提到此 SiP 工藝複雜性:雙面 Mold SiP,其 Full Mold 也是採用特殊定制的 Mold 模具,才能生產出階梯型的 Mold 面;同樣 250um 的 Mold 高度,50um 的 Gap,階梯形的 Mold 區域,對於 Mold 工藝和 Laser Mark 工藝都帶來極大的挑戰。
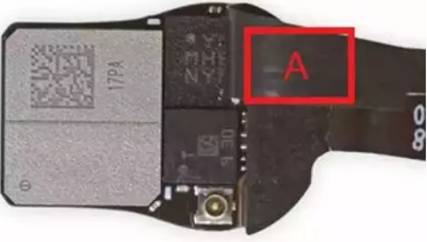
圖 14:階梯 Mold
5. 總結
經過上面的分析可以看到,這個做工精緻的小型化 Air Pods Pro 採用了多種 SiP 技術。這些會技術涉及到系統方案、設計模擬、工藝測試、材料及供應鏈等。
其中的 High Density SMT + MOLD + EMI Shielding;採用 Bottom 的那顆 Double Side Mold BGA 封裝,則把整個 SiP 模組的尺寸做得非常小,因而 SiP 的先進封裝技術在 Air Pods Pro 中起到了關鍵的作用。
因此在一個產品進行 SiP 模組設計時應從系統性、可加工性、電、熱等方面進行綜合的評估,這樣才能使產品更具競爭力。
因而提到 SiP 時就不能簡單地覺得 Air Pods Pro 小型化只是一個 SiP 技術了。
Apple 提出 Air Pods SiP(包括他提的 Watch SiP),絕不僅僅是針對非摩爾定律的 SiP 技術,而是涉及到系統方案、設計模擬、工藝測試、材料及供應鏈等一系列的 SiP 相關項。
如果沒有 High Density SMT + MOLD + EMI Shielding;沒有 Bottom 的那顆Double SideMold BGA 封裝,整個 SiP 模組的尺寸也做不到那麼小;整體的產品尺寸要求也無法實現,SiP 的先進封裝技術在 Air Pods Pro 中起到了很大的貢獻。
Apple 作為穿戴行業的引領者,一直走在行業的前面,引領了很多很多新的技術,同時,也引入了很多新的概念和想法。
產品的開發都要的預研,如 Air Pods Pro 在 2019 年 10 月 30 號發佈,據稱其在 2017~2018 年就已經開展了工程技術驗證和工程樣機的試產。
因而 Apple 工作內部應該早就啟動了 Air Pods Pro 2 的 SiP 的開發,至於什麼時候上市發佈,得要看 Apple 的計畫了。
當然了,Apple 有他獨特的優勢,這可能是其他的 TWS 耳機廠所無法比擬的。
因而開發一個 SiP 的產品時,能力較強的廠商可考慮下面的觀點:
體量大,可以引導晶片開發商單獨定制; |
|
單品售價高,利潤高,敢於嘗試新的技術和工藝; |
|
自己開發核心晶片,可以根據自己的節奏去開發新的產品; |
|
敢於沉澱。技術,是需要積累的。 |
相信,就像 2018 / 2019 年,大家一窩蜂地模仿 Air Pods 開發軟硬結合板的 TWS 耳機一樣。2020 年,會有很多很多公司在開發 SiP 形式的 TWS 耳機。
建議各個廠家能更多地從 System 的角度去思考、去規劃 SiP 產品,而不僅僅只是從一個 Package 的角度去規劃 SiP 模組。
本文授權轉載出處: Amao_eda365
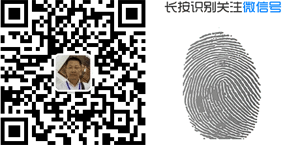